Diário de derramamento: Macondo, Deepwater Horizon
Em 20 de abril de 2010, um incidente no Golfo do México levou a um dos maiores derramamentos de óleo marítimo da história, quando a plataforma de perfuração semi-submersível, Deepwater Horizon, sofreu uma explosão submarina que resultou no naufrágio de todo o navio-sonda na água. Por meio deste Diário de Derramamento, examinamos nosso envolvimento nos esforços de resposta e as lições que aprendemos com este evento. Essas lições moldaram o cenário do derramamento de óleo e melhoraram a capacidade da indústria de evitar que incidentes semelhantes aconteçam novamente.
Overview
On the evening that the incident occurred, a well control event allowed hydrocarbons to escape from the Macondo well onto Deepwater Horizon, resulting in several explosions and a large fire breaking out on the rig. 11 workers tragically lost their lives on the day, and 17 others suffered critical injuries as a result.
The fire continued to burn for a further 36 hours until the rig eventually sank into the sea. Hydrocarbons continued to flow from the reservoir through the wellbore and blowout preventer (BOP) for a further 87 days, causing a spill of national significance.
During the clean-up of process in the weeks and months that followed, we worked closely with local authorities and other organisations that specialised in this type of incident; dedicated dispersant assets from Marine Spill Response Corporation (MSRC) and Airborne Support Incorporated (ASI) were activated in the initial stages of this event.
Due to the sheer size of the leak, the response to this spill utilised half of our global stockpile of equipment and saw 70 members of OSRL staff deployed to the Gulf of Mexico on rotation for over 80 days.
Challenge
During our response to Macondo, we supported strategic planning, SCAT (Shoreline Cleanup Assessment Techniques) activities, aerial and vessel dispersant operations, SMART fluorometry, and liaison with stakeholders, with a large portion of our staff members involved in the overall operation.
Our involvement began a few days after the initial explosion with the dispatch of an Incident Commander to provide logistics support to the shoreline clean-up assessment teams. This was quickly followed by additional personnel providing support to the client in a variety of roles as the response unfolded.
The Macondo incident was one of the first spills we attended at a much more influential level than previously. Over 45,000 responders were involved in the overall effort from different organisations, and it was important for our Spill Response Specialists to be deployed in key positions within the response structure to benefit the mobilising party.
Aerial dispersant resources were some of the first on the scene. At about 2AM on April 21, 2010, the dedicated dispersant assets from the Marine Spill Response Corporation (MSRC) and Airborne Support Incorporated (ASI) were activated to respond to the incident.
All of the dedicated dispersant aircraft were quickly activated due to the potential magnitude of the spill.
Although hundreds of skimmers and in-situ burn vessels were operating, there were still large dispersible slicks that were not tackled by that resource. The 300-member Aerial Dispersant Team played a critical role in the Macondo response.
305 square miles were sprayed by dispersant aircraft within an 18,000 square mile operating area, which was a clear demonstration of the huge coverage that aerial operations can deliver and cementing aerial operations as a key tool for any future large spills.
The Macondo incident dramatically changed the industry and our approach to spills. Our team has evolved and developed more efficient working practices that have been used on subsequent incidents in the years following. As a direct response to this event, it was decided through the establishment of the Global Industry Response Group and the creation of the Oil Spill Response Joint Industry Project, that future industry requirements for aerial dispersant application should be reviewed. The industry needed to consider new aviation platforms, with a range of capabilities to support its global needs and operations for a faster response.
In 2013, we teamed with UK aero engineering firm T2 Aviation, part of the 2Excel Aviation group, to deliver two modified ex-FedEx Boeing 727-200s, one fitted with a dispersant delivery system with a capacity of 15,000 litres, comprising internal tanks, pumps and a spray bar to deliver dispersant liquid (TERSUS system), the first time a pure jet had been used for such a purpose. The successful completion of this project in 2016 marked a global first for both the oil spill response and aviation communities alike. The TERSUS Dispersant Delivery System is the first and only aerial dispersant system to be approved for operation from a large jet aircraft. Our Aerial Dispersant Systems remain a foundation of incident response.

Solution
Bryony Wood, now our Dispersant Technical Authority, was working as a Consultant/Senior Response Specialist at the time of the Deepwater Horizon spill. Bryony had worked for OSRL for five years when the call came in to attend this incident, before which she had studied Oceanography and Marine Biology at Southampton University. Less than a year before this event, Bryony was dispatched to the West Atlas spill in the Timor Sea, which gave her the skills and experience needed to tackle this: “I was deployed on 8th May into the Incident Command Post (CP) at Houma and requested to lead one of the SMART teams to carry out sampling and dispersant effectiveness monitoring using fluorometry equipment”, recalls Bryony.
“A coastguard team was already in place and carrying out monitoring, but they were not yet reporting the data that was collected. I developed a format for daily reporting of fluorometry data and observations, which both OSRL and the coastguard SMART teams consistently used throughout their deployment. Daily reports were submitted through the chain of command to Houma CP to justify the continued and effective use of dispersant application as one of the most impactful techniques employed during the response. On a day-to-day basis, SMART teams were usually tasked through a spotter aircraft to a location to carry out monitoring on a slick before and after dispersant was applied by spraying aircraft.”
Occasionally, OSRL’s SMART team, which also had our vessel with onboard spray equipment, was asked to target a specific area of the oil slick and carry out a small-scale “test spray.”
As time progressed, our purpose evolved as we looked at ways to improve the effectiveness of the monitoring we could deliver. Further down the line in the spill, Bryony was asked to investigate the addition of particle size analysis to the monitoring being undertaken.
She added: “The purpose of the SMART team was to provide semi-quantitative data back to the CP daily so that the decision to continue to spray could be backed up by up-to-date monitoring and observation. This data was understandably under a great deal of scrutiny to ensure that dispersant was used appropriately and equipped those in the CP for their regular justification discussions with regulators.”
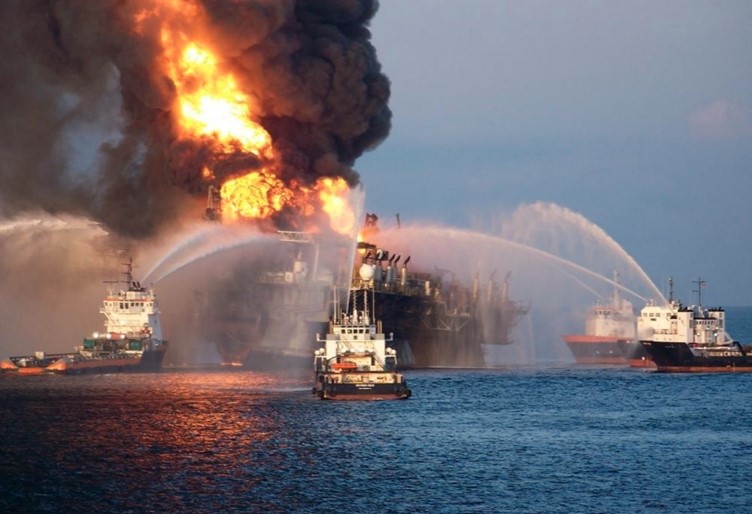
Impact
The impact of the Deepwater Horizon event was significant and visible through the statistics and figures that transpired in the months and years after.
Dave Rouse, our Country Lead / SCAT-Ops Liaison Manager at the time, was mobilised in early May to Louisiana to support the Shoreline Response Programme, concluding his time on the incident in December - nearly 8 months later, having worked across four of the five impacted states:
“My first role was Shoreline Cleanup and Assessment Teams (SCAT) Logistics and Safety Lead, in which I was responsible for planning and coordinating logistics to ensure SCAT could safely and rapidly access sites that needed surveying."
“At the peak of the programme there were 10-15 teams deploying to locations hundreds of miles apart and often very remote. A typical ‘commute’ for them could easily involve travelling by car, airboat, and helicopter.”
Working closely with a responder from the local area, Dave set up the SCAT safety and emergency response frameworks for the infield teams, ensured that they had safety and communications equipment, provided them with weather and situational updates, and coordinated short-notice missions and emergencies. Although it was little over a decade ago, communications were largely conducted by radio as teams were often outside mobile phone coverage, and it was in the days before smartphones were prevalent.
The SCAT/Ops Liaison role was crucial in ensuring alignment between the Planning and Operations teams, making sure the very specific and often technical shoreline treatment recommendations were implemented as intended by contractors in Operations who may have limited prior oil spill knowledge. In this scenario we were troubleshooters, translators, tacticians, and our famously described by our client as being ‘Force Multipliers’ with disproportionate impact. The work we did contributed to the establishment of the SCAT/Ops Liaison role in standard shoreline response good practice.
As the response evolved, Dave took on broader coordination roles within the Shoreline Programme, ultimately managing 30 OSRL responders and subcontractors deployed as SCAT/Ops Liaisons in Alabama, Louisiana, and Florida.
Following the Macondo spill, Dave worked for BP for three years, running a major project to establish oil spill response capability for a new country exploration programme in Libya and returned to OSRL in 2014.
It affected many of the areas surrounding the spill, including various ecosystems and wildlife, which had been severely impacted by the event. Over 1,200 seabirds were cleaned and cared for in a specialist unit before being successfully re-released into the wild.


Lessons Learned
The Macondo incident also led to the creation of the Subsea Well Response Project (SWRP), a non-profit joint initiative between several major oil and gas companies working together to enhance the industry’s capacity to respond to subsea well-control incidents.
Part of the problem in 2010 was that a succession of well-capping methods failed to stop the leaks, in two separate locations. This turn of events, as well as being unfortunate for the response in general, strongly influenced the media coverage and, hence, public opinion.
Our own Subsea Division was established in the wake of Macondo. This has led to the creation of our four capping stacks, stored in the strategically effective locations of Brazil, Singapore, South Africa and Norway. The incident also paved the way for the OSPRAG capping device, one of the most effective measures to strengthen the UK’s oil spill response capability. The device is designed to seal off a subsea well and regain control in the event of a blowout.
“As industry technologies and best practices evolve, which they have been doing at pace since Macondo, OSRL services have developed with them, so that our members remain prepared should there be another event.” OSRL SWIS Director, Andy Myers.
SWIS (Subsea Well Intervention Service) is now one of several OSRL supplementary agreements. SWIS membership provides access – internally and through various mutual aid frameworks - to a full suite of equipment, including the capping stacks, along with materials, vessels, and personnel resources to assist in the development of a comprehensive Source Control Emergency Response Plan (SCERP).
Extensive industry agreements and cooperative working practices since Macondo have reduced the chances of similar incidents and the likely effects on the environment if a similar incident should ever reoccur.
We’ve also played a key role in the move towards a cleaner industry, building on our range of Member Response Services, which include access to the Duty Manager at any time, logistics support with our aircraft to transport equipment, or access to chartered aircraft as we act as an agent, a stockpile of dedicated oil recovery equipment and dispersants, wide-area high-volume aerial dispersant spraying capability and a pool of expertise with a broad and in-depth range of skills.
As a direct result of Macondo, we developed the 5 x 5 on-site technical advice service, which provides up to five personnel for up to five days, completely free of charge, to encourage our members to engage with us from the very beginning. Prevention is always better than cure, so the 5x5 service also extends to prevention and preparedness advice. Members have used these five free days to provide valuable benefits from incident management coaching to wildlife planning. 5x5 is just one of a wide and increasing range of OSRL Member Benefits.
The sheer size of the Macondo spill clean-up operation, including the funding investment and personnel involved, provided a great deal of valuable ‘on the ground’ experience with new technologies and techniques evolving from this incident while also leading to increased funding for response technologies.
The main lesson that this event has taught the industry, including our membership, is that preparedness is key and all eventualities should be considered. The spill came off the back of four decades of ever-decreasing incidents. While it is true that even with the safety protocols of 2010, it took several factors to all go wrong at once, and safety checks and balances have been hugely tightened up since then, but it’s taught us that we must continue to train and equip for these ‘worst case scenarios.’